In another thread, I was asked to post some photos of the 4" S&D piping network I recently installed for my dust collection system. Ergo, here they are.
PHOTO 1 shows the connection of the two main trunks, upper and lower, to the impeller inlet on the dust collector via a single wye fitting. The hose at right serves the band saw -- see also Photo 4. It terminates in a standard quick-disconnect hose end fitting, which is a very snug fit inside the bell end of a 4" S&D fitting. The bare end of the hose will also fit, but is difficult to insert and remove. I chose to use the QD fitting in case I ever need to move the band saw completely out of the way.
The few small chips you see on the jointer's infeed table are the most that ever escapes the DC system at this tool. A system such as mine cannot possibly capture all the fine dust generated in a wood shop, but it's terrific at large-chip collection.

PHOTO 2 shows how the bottom half of the main trunk comes off the impeller inlet and heads off to serve the jointer and cabinet saw. I'll revisit this part of the system a little later in your tour. For now, note how the wye fitting is inserted into the impeller cover of my Harbor Freight 2HP dust collector. The ~4-1/2" OD of the wye fitting, wrapped with some 1/4" thick weatherstripping, made for a perfect fit.

PHOTO 3 is a shot of the currently-unused takeoff that will eventually serve a new router station that'll be incorporated into the extension wing of the cabinet saw ("A"), the connection for the saw itself ("B"), and at right, the connection for the jointer ("C"). This is the only portion of the ducting that is on the floor. Floor runs can be a tripping hazard; but since this one is not in a major traffic aisle, it's hardly the worst compromise in my shop.

PHOTO 4 shows how the hose in Photo 1 wraps around the back side of the band saw makes its connection to the tool. Since the band saw is on a mobile base, this piece of hose is the longest (but only by a few inches) in the entire system. I don't actually roll the band saw around the shop, but rather just rotate it in place in order to gain more infeed room, or to get it out of the way when I bring out the thickness planer you can see sitting on its mobile cart in the background.

PHOTO 5 is taken at the exact center of the shop. I placed the three primary vertical drops in the system at the three pipe columns that run down the center of the shop. The pipe labeled "A" serves the miter saw, out of the picture to the left. "B" is the port for the drum sander, and "C" is where the thickness planer connects when I roll it out into position for use. "D" is the main trunk, continuing on its way to the router table and points beyond. Note how the blast gate for the miter saw's run is placed as near the main trunk as possible, rather than over next to the saw. Ideally, you want the DC sucking on as little empty pipe as possible.
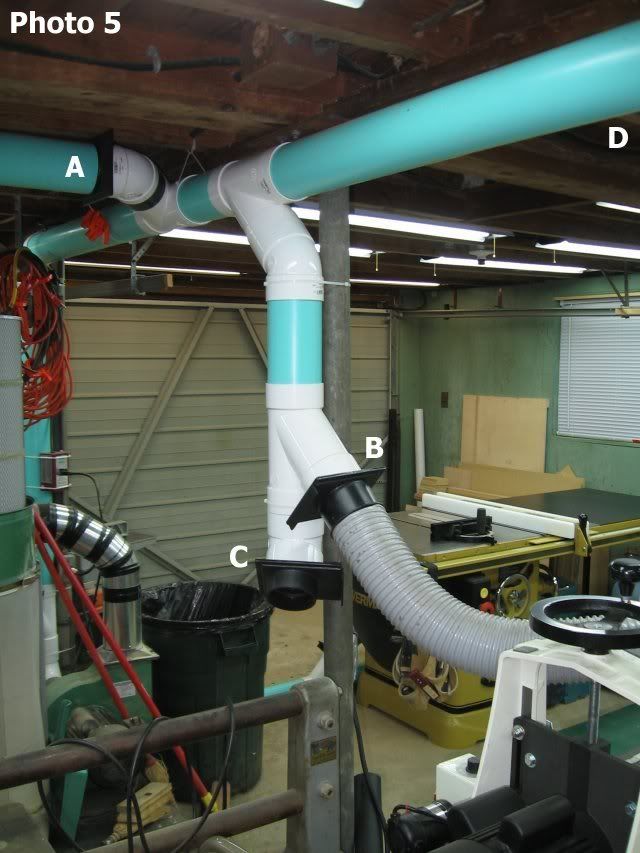
PHOTO 6 shows the drop at the miter saw. The dust on the horizontal surface is proof that trying to capture the dust from a miter saw is mostly futile without some kind of hood around the back side of the saw. The hose is longer than it needs to be; this is a temporary setup that will soon be replaced by an all-new miter saw bench similar to the one Nahm has in the New Yankee Workshop.

PHOTO 7 shows how the main trunk ("A") has a branch leading down to serve the router table fence ("B"), then on down to the router box under the table ("C"), while the main trunk itself continues on to the last drop in the system, above the countertop at the rear of the shop ("D"; also see Photo 8). Note how the piping is secured to the supporting structure with zip ties. Most of the pipe joints are just press-fit together, with no glue; at a few locations, I used a wrap of Gorilla Tape to hold things together. But for the most part a friction fit is adequate. The only real problem area is that the tapered flange on the plastic blast gates I'm using are prone to coming adrift of the fitting into which they are inserted. I'm going to secure them with some 1/4" long sheet metal screws.

PHOTO 8 is the dual 2-1/2" drop for the spindle sander and the shop vac hose that I use for general shop clean-up. I can also use the downward-facing blast gate to connect a router or sander, if desired. This is the farthest point in the system from the dust collector.
Yeah, yeah, I know: that sink in the background looks like something a truck stop men's room wouldn't have. I inherited a pretty big mess in the rented building that now houses my shop; I'm still working on cleaning it up.

PHOTO 9 shows the unused stub-out that I put in above the drill press to serve some future tool on this side of the shop, near the assembly table. I've no idea what that tool might be or where it would go, but the port is there in case I ever need it. In the background, you can see the pipe that runs over to the miter saw.

PHOTO 10 shows three things I'd change if I had it to do over (and I may change them anyway, since they kinda bug me). At "A" I would smooth out the awkward routing around the pipe column, a side effect of a late decision to raise the DC base platform a few inches off the floor so that it wouldn't roll around. At "B" I'd eliminate the short section of hose that I had to install because no available stock fitting gave me quite the needed angle. At "C" I'd extend the hard piping closer yet to the jointer's dust hood -- perhaps even all the way, replacing the hose entirely, since my jointer is not on a mobile base.

PHOTO 11 shows the biggest leak in the entire system. I need to remove my homemade stove pipe duct connecting the impeller housing to the bag inlet ring and seal the joint with weatherstripping. Most of the stray dust you see in the various pictures is coming from here.

And finally, PHOTO 12 shows -- or not -- the dust that escapes the DC system at the drum sander. I've only had this tool about six weeks but I've already used it a fair amount, and you're looking at the most stray dust I've ever seen anywhere near this tool. I will confess to being amazed at how well the DC works at this machine.

I'll be glad to answer any questions about any of the details of how the system is put together. Thanks for looking!
PHOTO 1 shows the connection of the two main trunks, upper and lower, to the impeller inlet on the dust collector via a single wye fitting. The hose at right serves the band saw -- see also Photo 4. It terminates in a standard quick-disconnect hose end fitting, which is a very snug fit inside the bell end of a 4" S&D fitting. The bare end of the hose will also fit, but is difficult to insert and remove. I chose to use the QD fitting in case I ever need to move the band saw completely out of the way.
The few small chips you see on the jointer's infeed table are the most that ever escapes the DC system at this tool. A system such as mine cannot possibly capture all the fine dust generated in a wood shop, but it's terrific at large-chip collection.

PHOTO 2 shows how the bottom half of the main trunk comes off the impeller inlet and heads off to serve the jointer and cabinet saw. I'll revisit this part of the system a little later in your tour. For now, note how the wye fitting is inserted into the impeller cover of my Harbor Freight 2HP dust collector. The ~4-1/2" OD of the wye fitting, wrapped with some 1/4" thick weatherstripping, made for a perfect fit.

PHOTO 3 is a shot of the currently-unused takeoff that will eventually serve a new router station that'll be incorporated into the extension wing of the cabinet saw ("A"), the connection for the saw itself ("B"), and at right, the connection for the jointer ("C"). This is the only portion of the ducting that is on the floor. Floor runs can be a tripping hazard; but since this one is not in a major traffic aisle, it's hardly the worst compromise in my shop.

PHOTO 4 shows how the hose in Photo 1 wraps around the back side of the band saw makes its connection to the tool. Since the band saw is on a mobile base, this piece of hose is the longest (but only by a few inches) in the entire system. I don't actually roll the band saw around the shop, but rather just rotate it in place in order to gain more infeed room, or to get it out of the way when I bring out the thickness planer you can see sitting on its mobile cart in the background.

PHOTO 5 is taken at the exact center of the shop. I placed the three primary vertical drops in the system at the three pipe columns that run down the center of the shop. The pipe labeled "A" serves the miter saw, out of the picture to the left. "B" is the port for the drum sander, and "C" is where the thickness planer connects when I roll it out into position for use. "D" is the main trunk, continuing on its way to the router table and points beyond. Note how the blast gate for the miter saw's run is placed as near the main trunk as possible, rather than over next to the saw. Ideally, you want the DC sucking on as little empty pipe as possible.
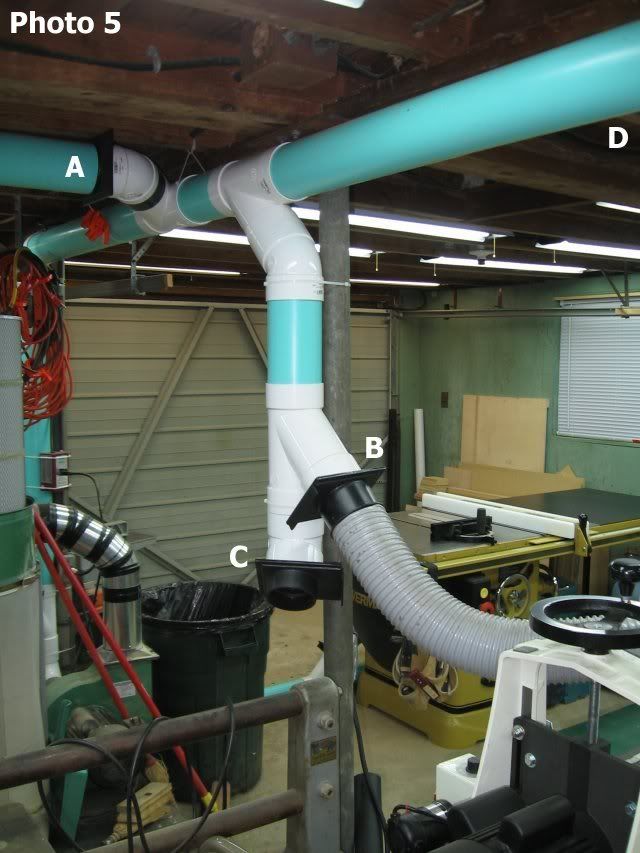
PHOTO 6 shows the drop at the miter saw. The dust on the horizontal surface is proof that trying to capture the dust from a miter saw is mostly futile without some kind of hood around the back side of the saw. The hose is longer than it needs to be; this is a temporary setup that will soon be replaced by an all-new miter saw bench similar to the one Nahm has in the New Yankee Workshop.

PHOTO 7 shows how the main trunk ("A") has a branch leading down to serve the router table fence ("B"), then on down to the router box under the table ("C"), while the main trunk itself continues on to the last drop in the system, above the countertop at the rear of the shop ("D"; also see Photo 8). Note how the piping is secured to the supporting structure with zip ties. Most of the pipe joints are just press-fit together, with no glue; at a few locations, I used a wrap of Gorilla Tape to hold things together. But for the most part a friction fit is adequate. The only real problem area is that the tapered flange on the plastic blast gates I'm using are prone to coming adrift of the fitting into which they are inserted. I'm going to secure them with some 1/4" long sheet metal screws.

PHOTO 8 is the dual 2-1/2" drop for the spindle sander and the shop vac hose that I use for general shop clean-up. I can also use the downward-facing blast gate to connect a router or sander, if desired. This is the farthest point in the system from the dust collector.
Yeah, yeah, I know: that sink in the background looks like something a truck stop men's room wouldn't have. I inherited a pretty big mess in the rented building that now houses my shop; I'm still working on cleaning it up.

PHOTO 9 shows the unused stub-out that I put in above the drill press to serve some future tool on this side of the shop, near the assembly table. I've no idea what that tool might be or where it would go, but the port is there in case I ever need it. In the background, you can see the pipe that runs over to the miter saw.

PHOTO 10 shows three things I'd change if I had it to do over (and I may change them anyway, since they kinda bug me). At "A" I would smooth out the awkward routing around the pipe column, a side effect of a late decision to raise the DC base platform a few inches off the floor so that it wouldn't roll around. At "B" I'd eliminate the short section of hose that I had to install because no available stock fitting gave me quite the needed angle. At "C" I'd extend the hard piping closer yet to the jointer's dust hood -- perhaps even all the way, replacing the hose entirely, since my jointer is not on a mobile base.

PHOTO 11 shows the biggest leak in the entire system. I need to remove my homemade stove pipe duct connecting the impeller housing to the bag inlet ring and seal the joint with weatherstripping. Most of the stray dust you see in the various pictures is coming from here.

And finally, PHOTO 12 shows -- or not -- the dust that escapes the DC system at the drum sander. I've only had this tool about six weeks but I've already used it a fair amount, and you're looking at the most stray dust I've ever seen anywhere near this tool. I will confess to being amazed at how well the DC works at this machine.

I'll be glad to answer any questions about any of the details of how the system is put together. Thanks for looking!
Comment